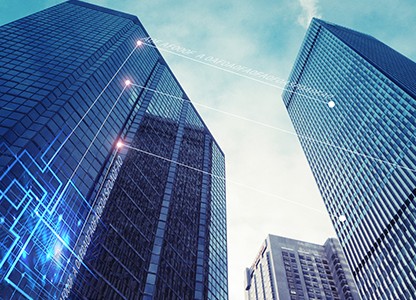
Types and causes of damage of deep hole rock drilled carbide tips
The damage of the deep hole rock drilled carbide tip is mainly caused by the fracture of the bit body and the damage of the cemented carbide sheet.
(1) Bit body fracture
The main fracture site is the front blade, the fin and the head and the joint are broken. The main reason for the fracture is that the strength of the bit body is not enough, the design section size is too small, and the forging temperature is too high or too low. Therefore, in the manufacture of the bit, in addition to ensuring a reasonable design size, the forging temperature must be strictly controlled. At present, most of the bit body materials use 40Cr steel, the forging temperature should not exceed 1250C, and the heating time in the furnace should not exceed two hours. If the temperature of the individual workpiece is too high, it can be forged after the billet is cooled to 1250C.
(2) Carbide sheet damage
The drill head for the downhole rock drill is working under heavy conditions. In the rock below the medium hard, the damage rate of the alloy sheet is about 5%, the damage rate is about 10% in the hard rock, and the damage rate is 20% in the extremely hard rock.
The main types of damage to cemented carbide sheets are:
Crushing
The entire length of the leading edge is broken along the edge. The reason for the chipping is that the height of the cutting edge is inconsistent. In use, the high-blade portion is subjected to full impact load and axial pressure, thus chipping. Therefore, after the bit is sharpened, the special gauge is used to check whether the blade faces of the fins are on the same plane, and the height of the control should not exceed 0.1 mm, which can basically eliminate the phenomenon of chipping.
Collapse
Most of the collapse angle occurs on the wing edge. Mainly because the alloy sheets are not inlaid, and some are extended too much. During the rocking process, the single wing contacts the wall of the hole, causing the alloy sheet to collapse. Therefore, the alloy sheet should be prevented from shifting during the insert. Generally, the amount of protrusion should not exceed 0.5 mm. When applying special gauge inspection during grinding, the radius of each part of the fin should be the same, and the deviation should be within 0.1 mm. After taking such measures, the phenomenon of sag can be greatly reduced.
Fragment
In deep hole rock drilling, the proportion of broken pieces is large. Mainly because the bit is under working, it is subjected to high impact load and the working stress is large; secondly, when the welding is pressed, the blade generates internal stress. Under the combined action of two kinds of stresses, the intermediate crack fragments are caused.